Railway Predictive Maintenance
Railway Predictive Maintenance
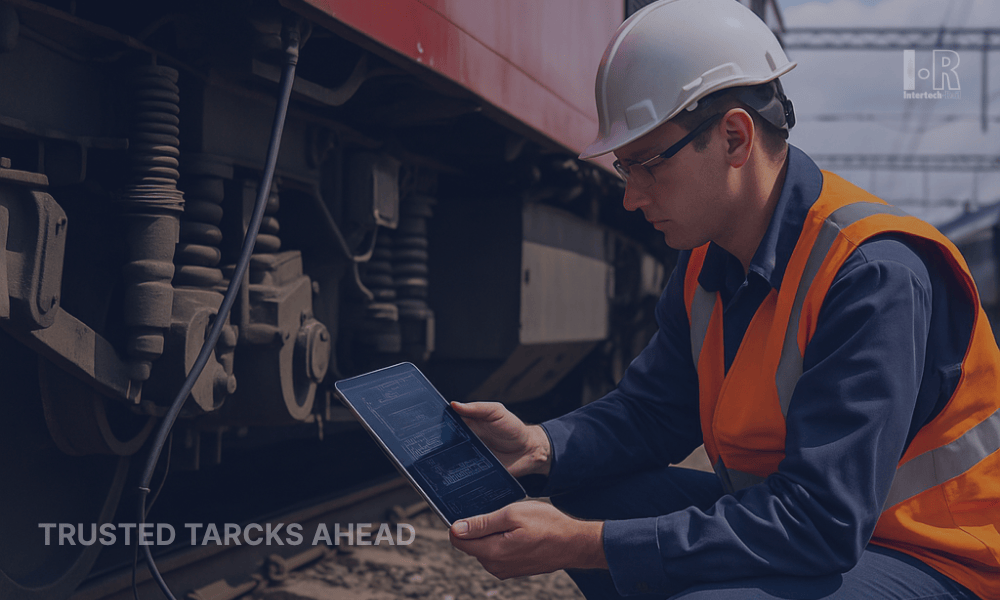
There has always been a delicate balance involved in keeping trains on track, both literally and figuratively. That used to entail repairing items once they broke or doing strict component inspections. However, railroads are becoming more intelligent these days. With the use of intelligent software
and small sensors, predictive maintenance is assisting operators in staying ahead of issues.
The True Meaning of Predictive Maintenance
Predictive maintenance
employs real-time data to identify early warning indications of issues rather than waiting for a breakdown or depending on routine inspections. A slight increase in temperature or an odd vibration might not seem like much, but these could be the first signs that something is ready to break. Early action on the data saves a great deal of frustration, money, and time.
Why It Works
Trains and tracks are equipped with small sensors, frequently no larger than a dime. They provide operational teams with information by measuring variables including movement, pressure, and heat. Companies like
Intertech Rail
have developed systems that assist in collecting and organizing all of this data without interfering with day-to-day operations.
The system starts to see patterns as it gathers more data. Future maintenance teams will be alerted if specific indicators appear frequently just before a component fails.
The Reasons Behind Rail Operators' Attention
Crews spend more time staying ahead and less time reacting when they fix items only when necessary, and before they fail. This lessens the need for emergency maintenance and keeps trains rolling. It's safer, too. Accidents can be avoided by spotting a worn brake or a fractured component before it malfunctions. Additionally, trains are more dependable when they are safer.
How Everything Is Related
Sensor data must flow efficiently. Wireless technologies like 5G and LoRaWAN can help with it. Some systems even use micro-edge devices that send out immediate notifications to process data on-site.
Additionally, this data must interface with current systems. Crews aren't learning everything from scratch because a lot of predictive maintenance systems integrate with
SCADA
or ERP platforms. Field technicians may more easily respond to alerts, review logs, and report problems thanks to mobile apps.
Beginning Small and Growing Wisely
The majority of new rail businesses start by focusing on high-risk or high-value components. These pilot initiatives frequently demonstrate the idea rapidly, cutting down on delays and maintenance expenses. There is indeed a learning curve. Sensors require calibration, and teams require time to adapt. The advantages, however, are self-evident.
It's Functioning Already
Passenger trains in Europe are operating more smoothly and with fewer delays. These technologies are used by freight carriers in the United States to track lengthy routes and identify problems early, especially in isolated locations.
Predictive maintenance is a superior approach to maintaining complex systems, not merely a passing trend. Operators lower costs, increase safety, and maintain railroad operations by taking action before a fault occurs.
Additionally, implementing this strategy doesn't have to be difficult thanks to modular platforms and practical solutions from businesses like Intertech Rail. It only has to be sensible. Ultimately, trains function better when humans and technology collaborate. It is that easy.
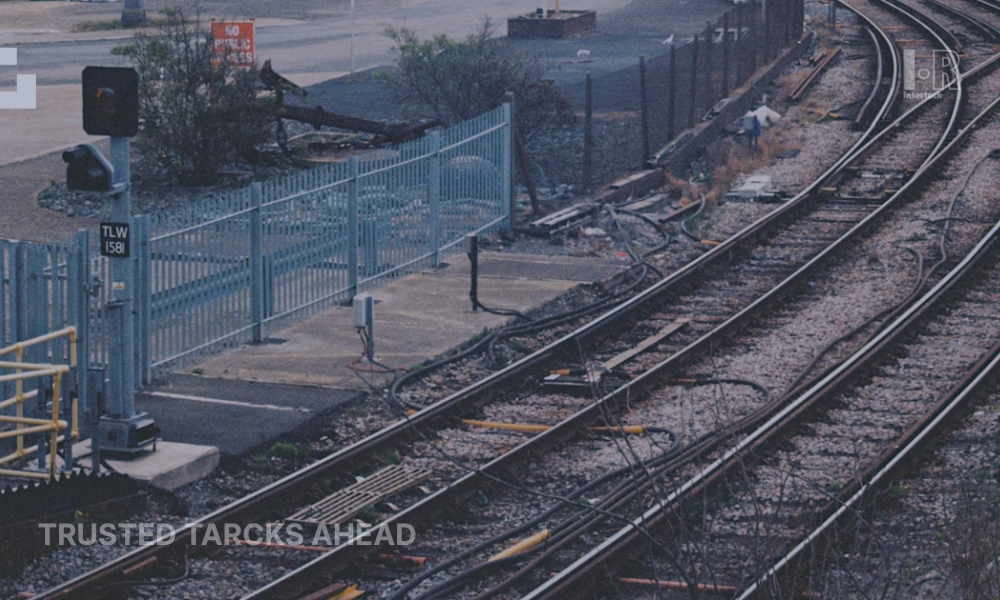