Vital Signaling at the Forefront: Innovative Methods for Ore Transport
Vital Signaling: technology that propels the production and the railway transportation of ore
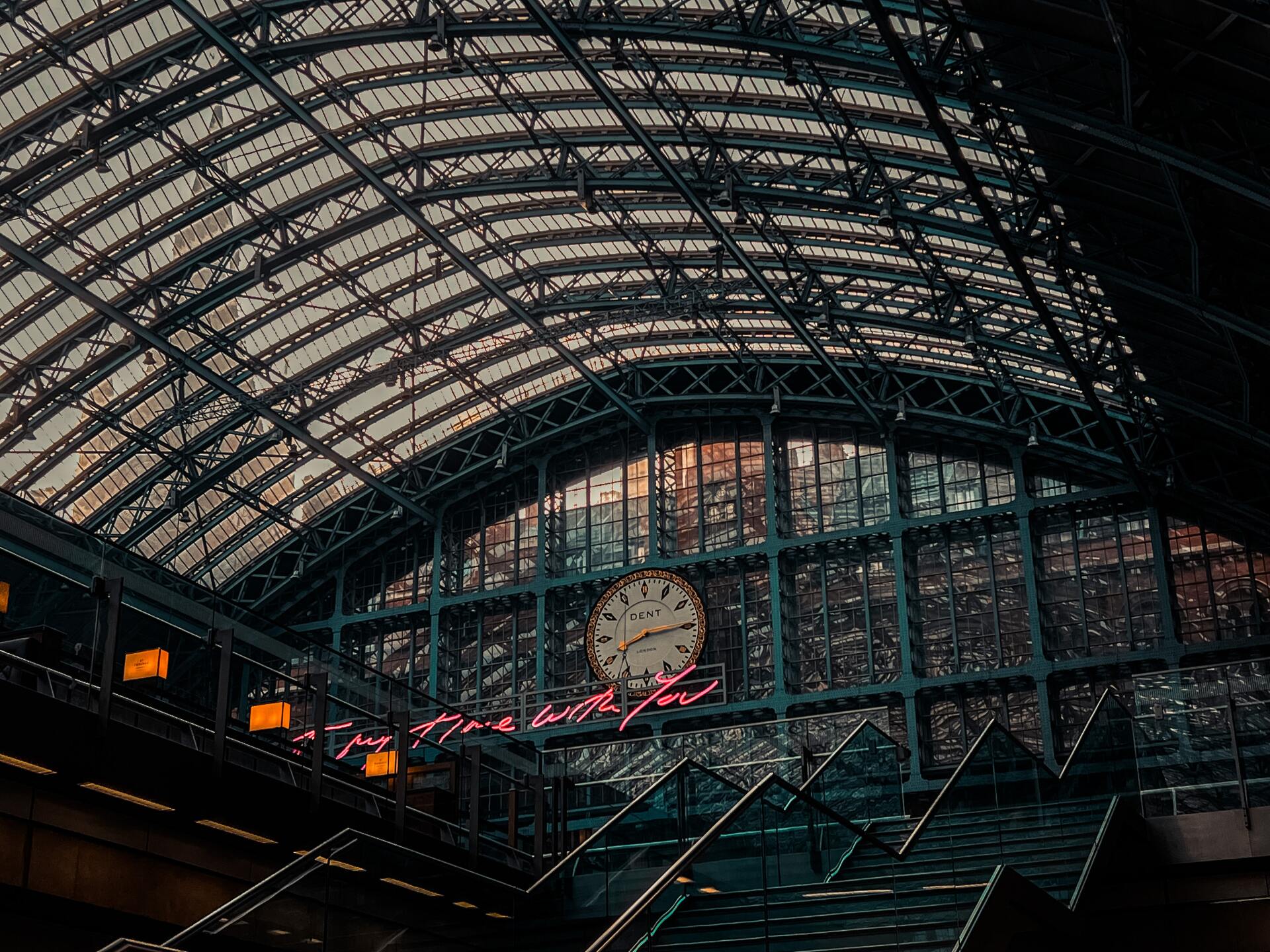
People say that those who own a shoe store have only to know how to sell shoes. And those who have restaurants, need only to know how to cook. But is it really true? If it is, then, those who own mining companies only needs to extract their ore and ensure profit. This easy? Wrong! The answer is a loud and categoric no! And do you know why? Because we need to talk about safety.
I will explain it. A major part of the mines need to have their ore transportation until the destination, be it a harbor, a factory or a client, and that must usually be carried out via railway network — once the transportation via trucks is not economically feasible. However, the operations in the railways are usually difficult and unsafe, with a huge risk of accidents that might occur. I myself have seen this happen a number of times.
Mainly in little developed countries of the Middle East, Africa and Latin America, it is common for the mining company to find an ore deposit (most of the times in locations the access to which is difficult) and assemble an extraction operation, installing a railway with a single locomotive for transporting their production. This railway starts its operation with a single train. The visual control is carried out on a manual basis by the operators and through the so-called Tracks Change Devices (TCD), under order given via radio from another operator that regularly makes the movements’ planning on a board (!). Now imagine if said ore has to be transported for about sixty miles, and this is a very conservative example in terms of distance. If the railways signaling is neglected, there is a big risk that the production does not reach its destination on account of accidents on the way.
Yet, despite not being as worrisome as the abovementioned example, it is only one locomotive. Now imagine that the company grows and starts to operate with three locomotives in the same railway network. With no signaling, such as traffic lights and route alignment, the operation, which was already potentially dangerous with one trains, starts to enter into an imminent accident risk zone, and that happens because rare are the cases in which the mining company invests in a railway safety specialist in order to solve problems before any accident might take place. Unfortunately, what we see out there is the higher and higher incidence of severe railway occurrences, many times of big proportions, interrupting the entire operation, generating millions in terms of financial losses (not to mention fatal accidents).
My experience as an entrepreneur and railway automation specialist shows that only three in ten railways in mines fulfil the minimal safety requirements. I am talking about Vital Signaling, also referred to as safe-failure system, which depends on minimal human interaction and therefore, exponentially decreases the occurrence of human errors in the metro railway transportation. The idea is that the movements start to be made via “route alignment”, i.e.: the train may only move if the way ahead is free and if the TCD are in their correct positions. And more: with signalers spread all over the tracks, showing a green light for the machinist to go on. In case of a red light, the train should immediately stop. This minimal level of safety, which, by the way, has a very low investment cost, might avoid 99.99% of the cases of accidents. But not even this is put into place.
Why? Well, at first because the company that controls the railway usually fails to perceive how the Vital Signaling, besides ensuring safety, is an instrument that increases productivity, since it allows for the trains to move faster and closer, with more ore flowing and increasing the profit. It is not perchance that the major mining companies of the world move their trains with onboard computers (ATC – Automatic Train Control), with no human interference, electric TCDs and RFID (Radio Frequency Identification) TAGs (labels), which show the situation of the railway network ahead, maximum speeds and the precise location [of the trains] along the entire tracks. Almost with no need for intervention from machinists, these trains move faster, accelerating and deaccelerating in a smart fashion, usually very close to each other, and with complete safety. Everything is controlled in the Operating Control Center (OCC), with a big quantity of indicators for the operation to be successful from one point to the other.
The investment in Railway Automation is mandatory for those who think in the long run and in the safety of the operation. It is an inevitable step for companies that wish to grow without sacrificing the production and human lives. More than that. It is a change of paradigm focused on the awareness that the Vital Signaling is not a concept, but a reality, which, by the way, is very easy to be implemented, even from the economic point of view. As incredible as it might sound, only one operating day stopped at the mine on account of a railway accident would already be enough to pay for the best signaling system available.
* Wilson Antunes is an entrepreneur and specialist in metro railway automation, and Engineer graduated by the Polytechnical School of the University of São Paulo (Poli-USP), as well as Business Administration by the Getúlio Vargas Foundation.